Es importante que aprendamos de los accidentes del pasado para poder prevenir que otros similares ocurran en el futuro. El caso de la ‘Corporación Caribeña de Petróleo’ (CAPECO) es muy interesante, hay muchas lecciones que podemos aprender de él para mejorar la seguridad de las instalaciones de almacenamiento de petróleo. El 23 de octubre de 2009, a las 12:23 am, ocurrió una explosión en la terminal de almacenamiento de petróleo de CAPECO en Bayamón, Puerto Rico. Durante el proceso de llenado de varios tanques con gasolina proveniente de un buque petrolero, desbordó uno de ellos, de diecinueve mil metros cúbicos (19.000 m³). La gasolina derramada formó una niebla que se extendió hasta la sección de tratamiento de agua de las instalaciones, donde ocurrió la ignición. Los múltiples incendios y explosiones que siguieron dañaron o destruyeron diecisiete tanques que contenían gasolina, combustible de avión y diésel. Ni CAPECO, ni el departamento de bomberos local contaban con el equipo o entrenamiento necesarios para enfrentar incendios de tal magnitud; y estos se extendieron durante casi sesenta horas hasta que finalmente se pudieron apagar. Los productos derramados contaminaron el suelo y el agua cercanos. La onda de choque dañó aproximadamente trescientos hogares y negocios, algunos, a más de dos kilómetros de distancia de los tanques. La instalación militar cercana, Fort Buchanan, sufrió daños equivalentes a cinco millones de dólares. Miles de personas tuvieron que ser evacuadas; afortunadamente, los trabajadores escaparon a tiempo, y no hubo muertos, solo tres heridos.
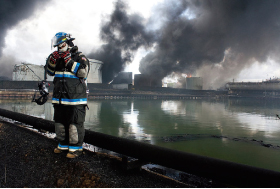
Reporte de la CSB
La Comisión de Seguridad Química de Estados Unidos (CSB) investigó el incidente, y publicó un reporte en 2015. Concluyó que, durante la transferencia de gasolina desde el buque cisterna, el tanque 409 se desbordó, lo que resultó en una nube de vapor que abarcó ciento siete acres (un acre igual a 4.046,85 metros cuadrados) de las instalaciones. La topografía permitió que la nube de vapor migrara a través de las válvulas abiertas de las barreras de contención secundaria hacia la zona de tratamiento de aguas residuales, donde se incendió. Entre las causas que contribuyeron al exceso de llenado, el informe enumera:
- Mal funcionamiento del medidor de nivel del tanque;
- variaciones normales en la presión y el caudal de gasolina proveniente del buque, sin la capacidad de la instalación para identificar estos cambios;
- potencial falla del techo interno del tanque;
- falta en los tanques de un sistema independiente de alarma de alto nivel, lo que daría una indicación visual o auditiva en caso de alto nivel, o un sistema de prevención de sobrellenado automático independiente;
- inadecuación de los procedimientos de llenado, que requerían que los operadores abrieran parcialmente la válvula de admisión de un tanque durante el llenado de otro, debido a que la presión hacía que fuera difícil abrir manualmente una válvula totalmente cerrada (esto aumentó el error en los cálculos de tiempo de llenado);
- debido al diseño de las válvulas, dificultad para distinguir entre las posiciones abierta y cerrada; e insuficiencia de la iluminación, que impidió a los operadores ver correctamente el sobrellenado y la nube de vapor.
CAPECO no se había preparado para un incidente con los servicios de emergencia locales ni había formado debidamente al personal de la instalación para hacer frente a un incendio de esta magnitud. La falta de coordinación entre las organizaciones que respondieron al incidente complicó aún más la respuesta de emergencia. La CSB dio cuenta de que las regulaciones estadounidenses no consideraban a las terminales de almacenamiento de petróleo como la de CAPECO como “instalaciones de alto riesgo”, y no exigían para ellas un sistema de alarma de nivel alto o un sistema de prevención de sobrellenado. La insuficiencia de los requisitos reglamentarios llevó a que CAPECO tuviera una instalación de alto riesgo.
La CSB indicó que, a pesar de los incidentes ocurridos en el pasado en Estados Unidos y en otros lugares del mundo, la respuesta de las organizaciones de estandarización había sido insuficiente para evitar incidentes similares. API 2350 solo requiere un sistema de prevención de sobrellenado automático (AOPS) para instalaciones operadas de forma remota, y no ofrece orientación sobre cómo realizar una evaluación de riesgos. Si CAPECO hubiera utilizado una alarma de alto nivel y AOPS, la alarma habría sonado, y la transferencia de gasolina se habría detenido automáticamente antes del sobrellenado. CSB recomienda la revisión de la Norma API 2350 para exigir AOPS en las instalaciones existentes y nuevas de tanques en superficie que almacenan gasolina, combustible para aviones, otras mezclas de combustible y otros líquidos inflamables que tengan un grado III o más de combustibilidad NFPA 704 (norma de la ‘Asociación Nacional de Protección contra el Fuego’ de Estados Unidos).
Conclusiones: ¿cómo podemos prevenir incidentes como CAPECO?
El incidente de CAPECO no es único. Desde el año 2005, ocurrieron tres incidentes de baja frecuencia pero graves consecuencias, que implicaron la formación de nubes de vapor desde tanques de almacenamiento de gasolina, dando lugar a explosiones e incendios catastróficos. La CSB indicó que el accidente de CAPECO podría haberse evitado si la instalación hubiera: llevado a cabo una evaluación de riesgos; incorporado los cambios basados en las lecciones aprendidas de incidentes similares anteriores; puesto en práctica más de una capa de protección, como un sistema de alarma independiente. (De acuerdo con la CSB, el costo de los sistemas de prevención de sobrellenado es mínimo en contraste con los costos sociales y económicos de incidentes como Buncefield y CAPECO).
En la figura al pie, se muestra un diagrama de Bowtie que analiza los riesgos de CAPECO. Podemos observar las barreras que se podrían haber aplicado, tanto para prevenir, como para mitigar las consecuencias del sobrellenado de un tanque.
En Bruno Schillig queremos mejorar la seguridad de las instalaciones de almacenamiento de petróleo, y por eso nuestro equipo de expertos ayuda a las empresas a analizar sus riesgos y realizar sus propios análisis de Bowtie, sin ningún cargo. Podemos prevenir los incidentes de sobrellenado con el uso de sistemas de prevención de sobrellenado (OPS), como nuestro sistema TSM, entre otras medidas de seguridad. Un buen OPS es una herramienta esencial, efectiva en casos de errores en la operación y de falla del la ‘medición de tanques atmosféricos’ (ATG) , como ocurrió en CAPECO. El incidente de CAPECO nos muestra que las terminales de tanques cerca de poblaciones residenciales son instalaciones de alto riesgo, y por lo tanto se debe realizar una evaluación de riesgos y utilizar múltiples capas de protección para proteger a los trabajadores y al público.
Se puede encontrar más información en el informe completo de la CSB; en su misma página web hay un video muy informativo sobre el incidente: www.csb.gov/caribbean-petroleum-refining-tank-explosion-and-fire/ Sobre el sistema de prevención de sobrellenado TSM: www.acuraflow.com
|